Hydraix II
High efficient urban concept fuel cell vehicle prototype
Our competitor for the season 2024
The idea of this years competitor was to improve reliability and efficiency using last years car as a base. We focused on the specifications and it should suit urban driving needs for one person. This vehicle was designed to consume as little energy as necessary. In addition to specially designed system components, a digital driving strategy has been developed to optimize driving performance on the track. For further optimization, lithium-ion capacitors were added to the system to provide a temporary energy storage.
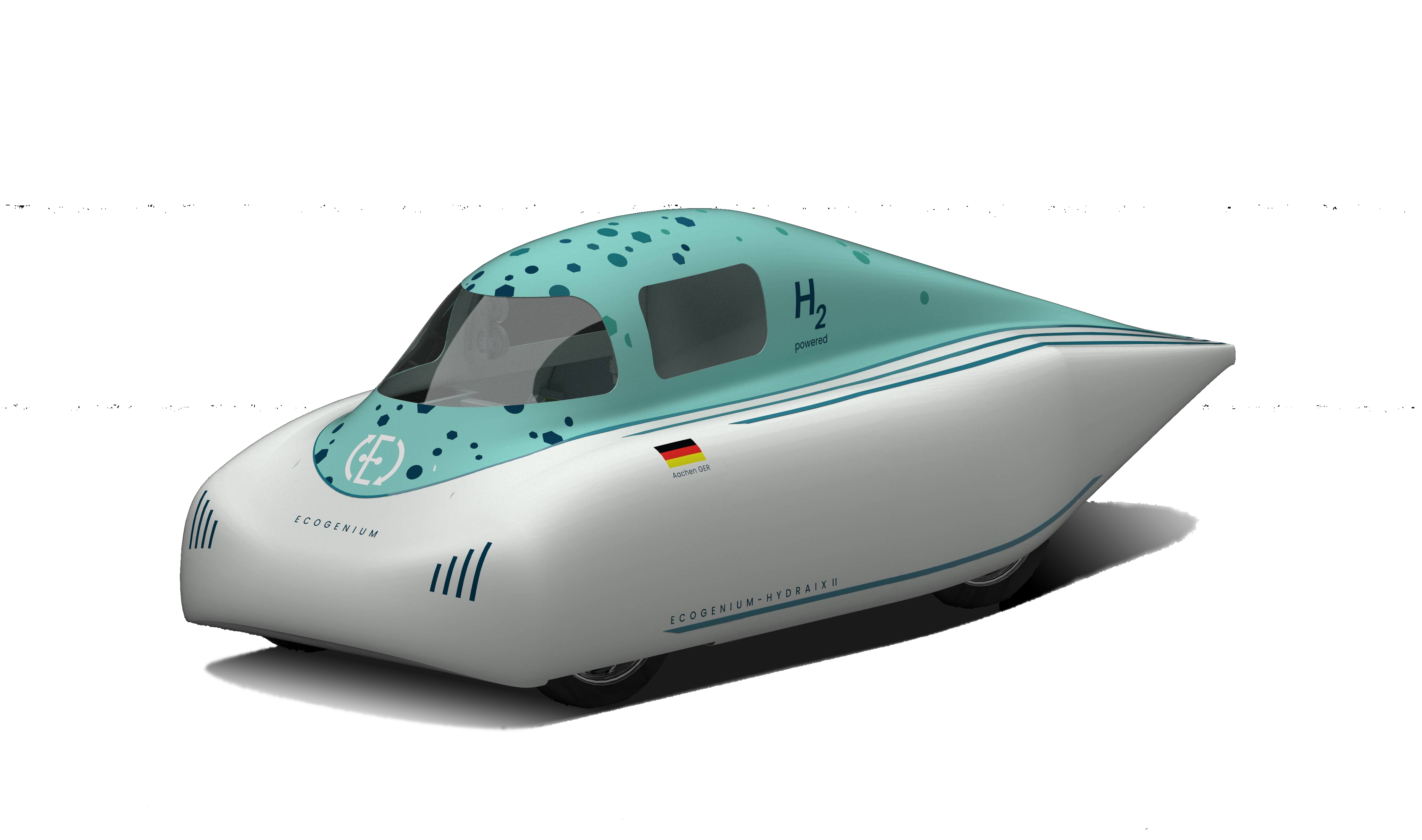
Quick facts:
- weigth: 102 kg
- max speed: 40 km/h
- energy conversion trough 1 kW air cooled PEM fuel cell
- consumption rate: 70.2 g/100km
- motor power: 2 x 280 W
Vehicle highlights
Fuel Cell System
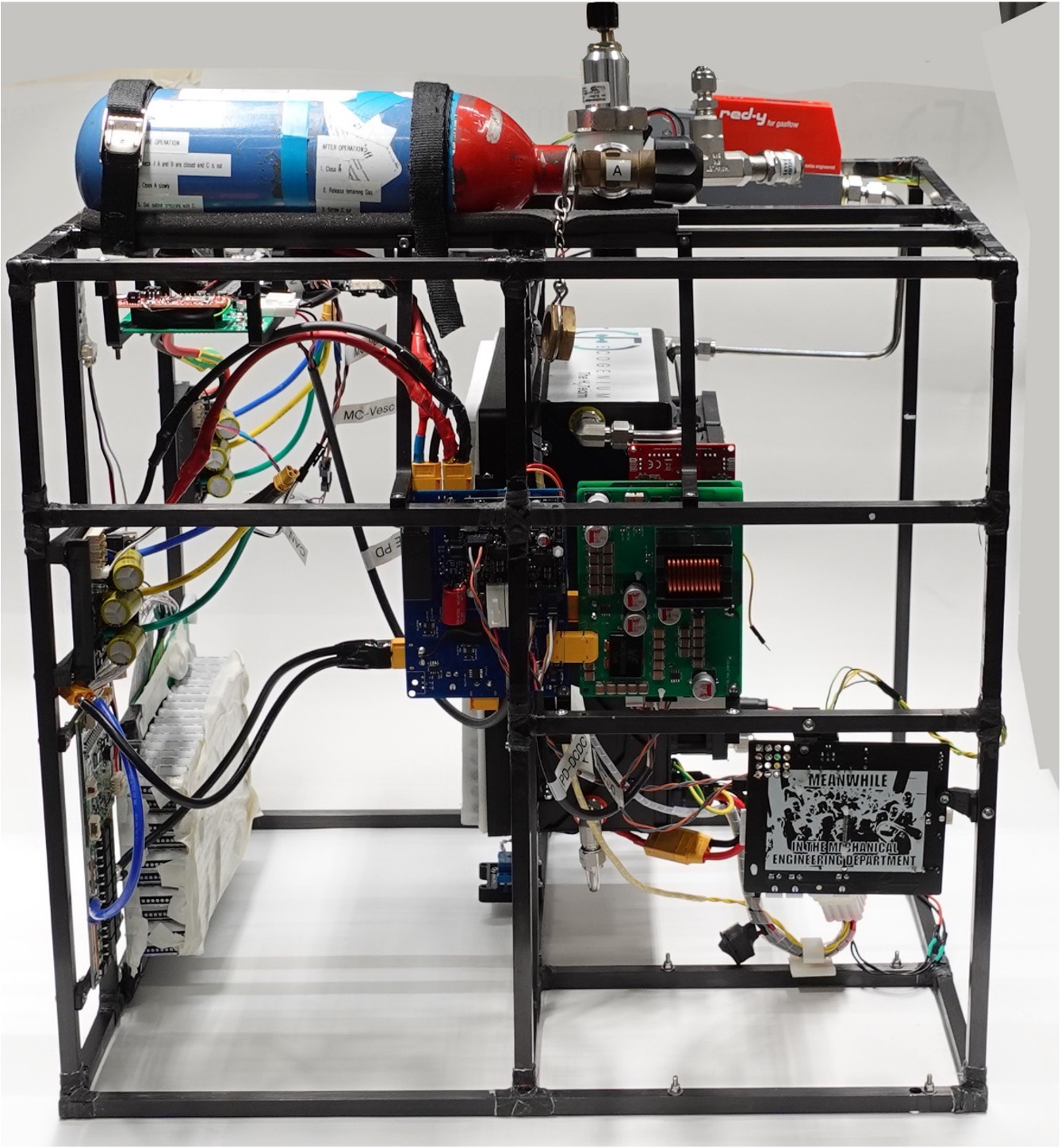
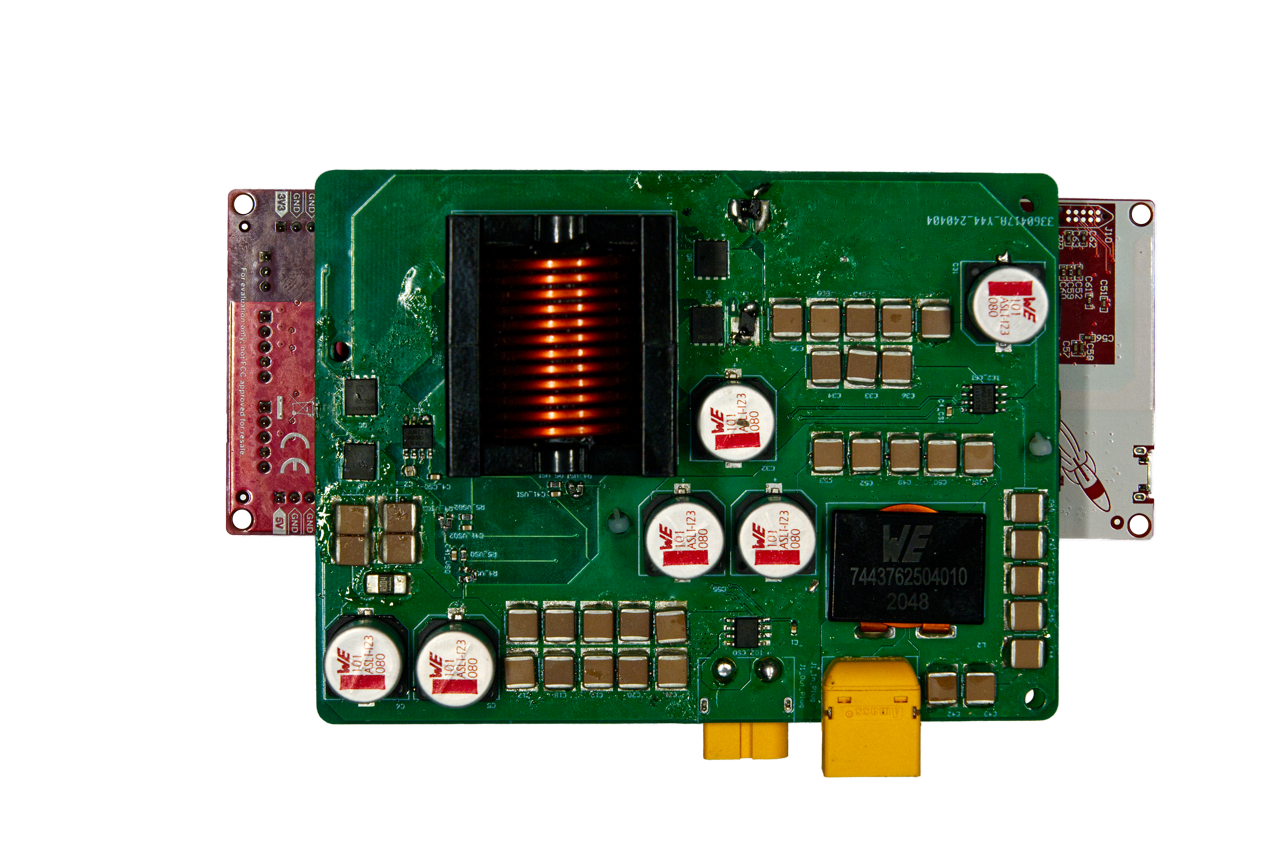
Electric System
Controlling and Driving Strategy
The heart of the control system is our Main Controller, which uses a separate RP2040 to run our strategy, controls all the other Bus Interfaces via CAN and directly controls our power system.
It also allows easy debugging, either via the display or by connecting a CAN module to it. This system integrates a 1 kW air cooled fuel cell into a directly controllable hybrid system, that is centrally controlled using a Simulink model running on a custom software stack.
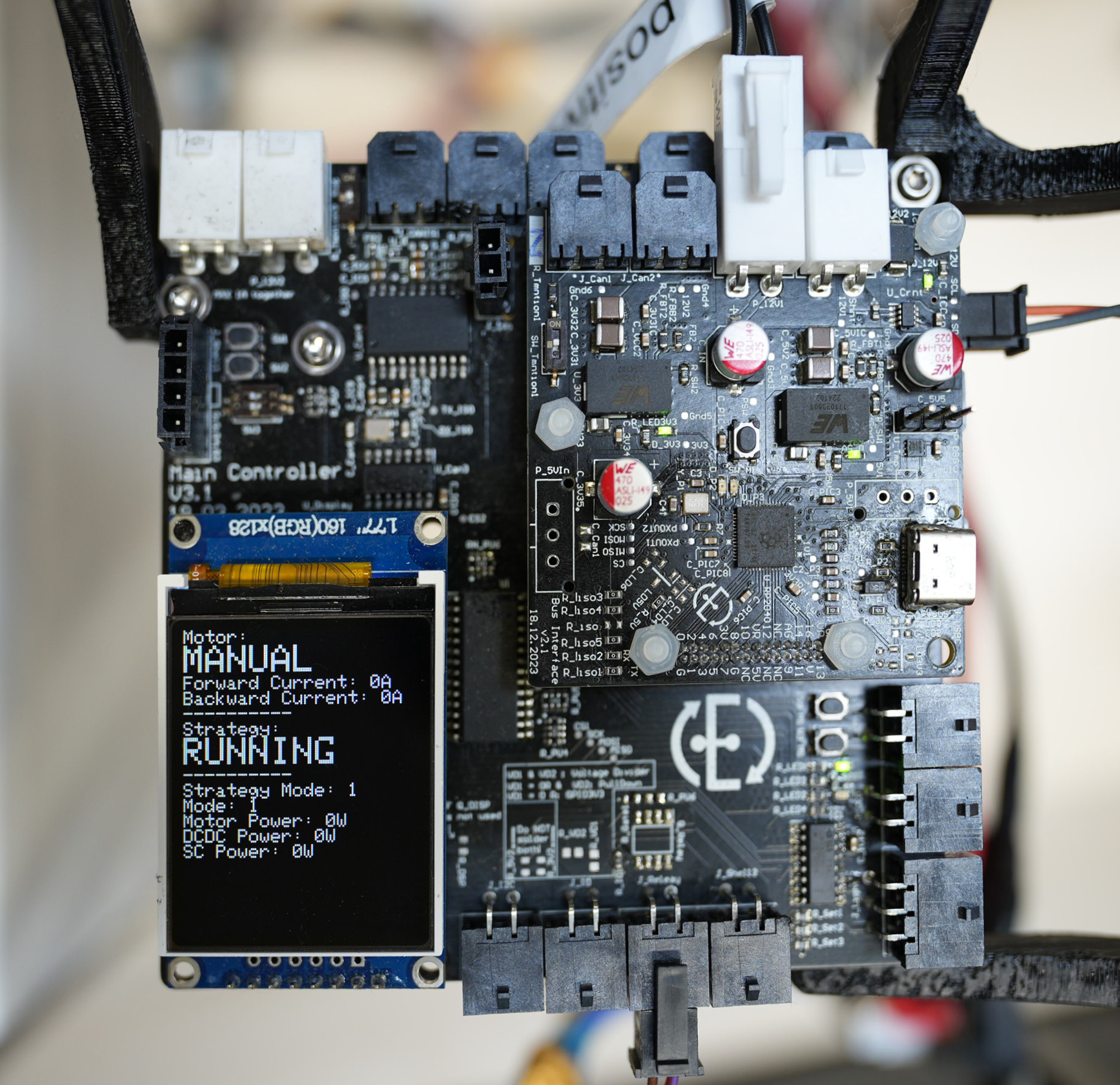
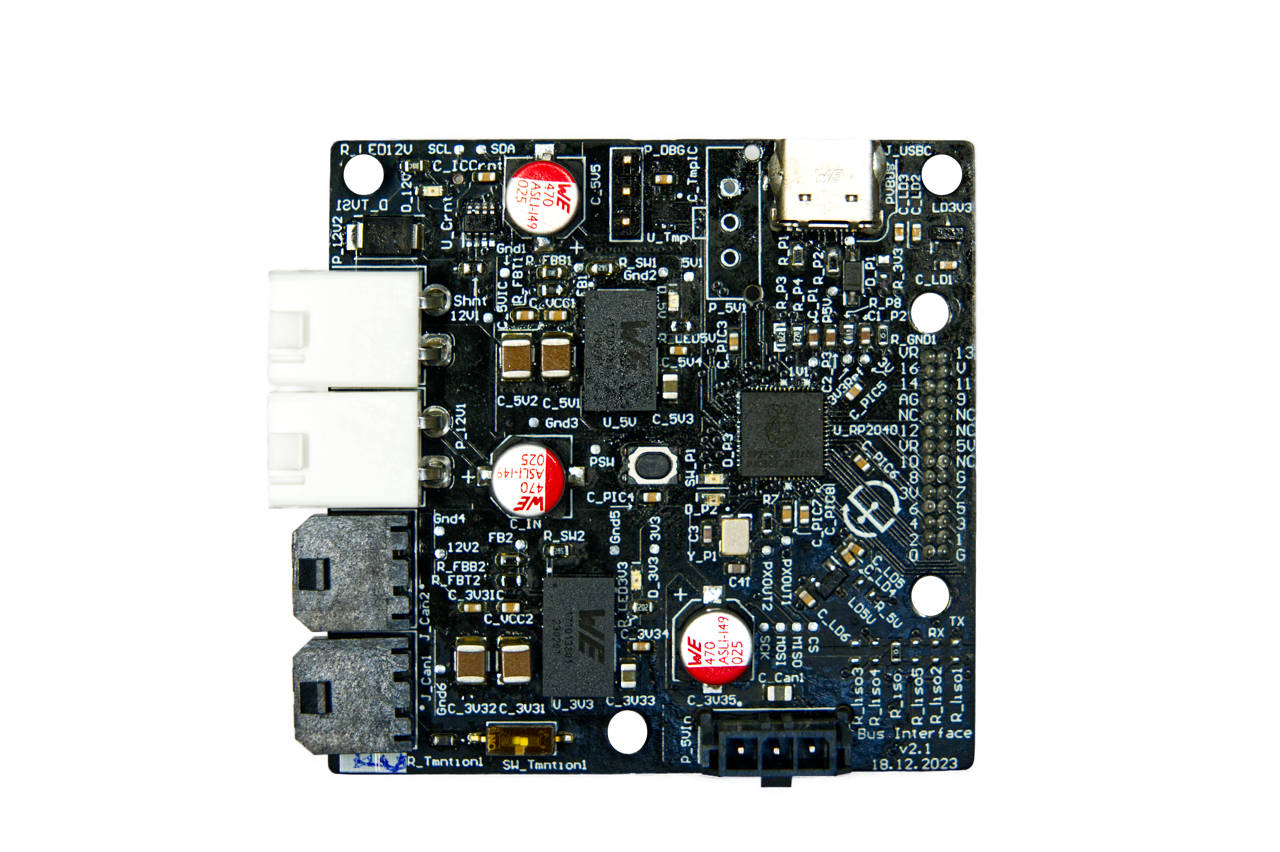
Bus Interface
In order to streamline the PCB design process, commonly required functions such as DCDC converters, CAN communication, power measurement and a microcontroller have been incorporated into the Bus Interface.
Hydraix II contains a total of 4 Bus Interfaces with different self designed shield PCBs.
In-house developments
Atava
Atava is a C++, freeRTOS based rapid prototyping system and forms the software of Hydraix. It is developed in a way that every hardware component can be individually implemented in a RTOS taks and tested without the rest of the system. Atava also makes CAN Bus communication, data logging and data injection during testing, easy. Every controller of Hydraix runs Atava as the base system and on top the individual hardware controlling and processing. Additionally, the main controller runs a compiled Simulink model, that interacts with all other controllers and acts as the control and driving strategy. Atava also natively implements an emergency mode which can be triggered and safely stops the whole system.
Super Capacitor System
To balance out peaks and valleys in power demand, we developed a system that is capable of storing energy in super capacitors and consequently releasing it. Combining the two energy sources takes a bit of effort in controlling, which we developed detailed models and strategies for. This makes Hydraix II a hybrid vehicle.
Steering Wheel
Our steering wheel is more than just a part that steers our car. With the steering wheel, you are able to control all the settings that are needed to drive the car on the track. You set the throttle, activate/deactivate the manual or automatic driving mode, control all the lights and see the actual energy of the super capacitors. You will also see the load that is provided by the fuel cell itself.
To achieve all that, we had to build our steering wheel completely by ourselves. The main structural part is a carbon backplate that gives excellent stability. On top of that is our 3D-printed cover, which holds the LCD and the required buttons. Our throttle is placed on the back for ergonomic handling while driving. All the signals come together in a custom PCB, which then transmits the data to the other hardware components.